Merchant Marine
Efficient, robust, durable. Meets all requirements of modern merchant shipping construction and evolving needs for energy saving.
Boilers & Economizers & ORC
ALFA LAVAL AALBORG
Inert Gas Generators
ALFA LAVAL AALBORG
Precise Tank Measuring
API MARINE
Fire Fighting
VTI
Incinerators
ATLAS INCINERATORS
ICCP & MPGS
ACG
HVAC&R and fans
DMA
Centrifugal Pumps
POMPE GARBARINO

Boilers & Economizers & ORC | Alfa Laval Aalborg
A century of experience in heat supply
Alfa Laval has one of the most extensive product ranges in the field of marine boilers. Their company’s experience dates back to 1919 when the first marine boiler was developed at the Aalborg Shipyard in Denmark. Boilers on ships are used for provide steam for various processes such as pumping, heating, cooling, cleaning and hot water for accommodation.
From waste heat to added value
Recovering waste heat is a unique opportunity that benefits both your bottom line and the environment. That’s why using exhaust gas to generate steam is so attractive, as 50% of the fuel energy of a main engine goes into the heat flow.
Alfa Laval’s Aalborg waste heat recovery systems have been proven to deliver fuel savings and CO2 reductions of up to 14%. Thanks to our extensive experience, we can design and install systems that maximize energy gains without compromising onboard safety.
In addition to heat recovery from the main engine exhaust, Alfa Laval is expanding the Aalborg portfolio by focusing on previously neglected waste heat sources. Today, waste heat recovery from auxiliary engine exhaust can cover steam requirements during port calls and in some cases even at sea.
Oil fired boilers & combi boilers
The Aalborg oil-fired boilers and combi boilers are highly efficient boilers designed for steam generation. They are designed for high efficiency, are user-friendly, self-cleaning and environmentally friendly to maintain.
The oil-fired boilers are equipped with an advanced touchscreen control system that enables convenient operation by the crew.
To be ready for the future, the modern boiler designs will be equipped with multi-fuel burners to to cope with the unpredictable future of upcoming fuels in all forms e.g LNG, methanol and ammonia.
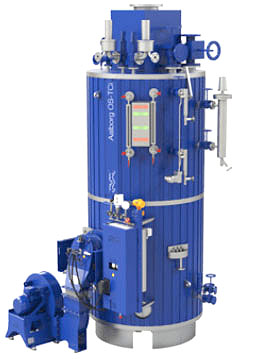
Exhaust gas boiler & economizers
The Aalborg economizer is designed to use the exhaust gases from diesel engines to generate steam. The design is customized according to the exhaust gas requirements and temperature. The economizers are supplied with their own steam space or can be connected to a boiler to use another existing steam space.
Smaller exhaust gas economizers are specially designed for auxiliary engines. They are designed to significantly reduce oil consumption for the oil-fired boiler.
The exhaust gases from auxiliary engines have previously been an overlooked source of energy. However, as the cooler exhaust gases from long-stroke main diesel engines may not be sufficient to meet steam requirements, they are becoming increasingly attractive. The exhaust from the auxiliary engines can meet the steam demand while in port or even while underway. With today’s high fuel prices, such exhaust gas economizers usually pay for themselves in 1-1.5 years.
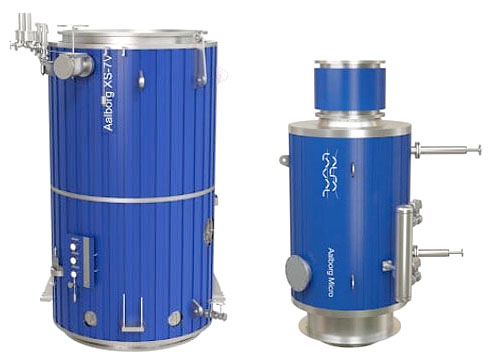
Thermal Oil Heaters: Aalborg TFO & Aalborg EX
Alfa Laval Aalborg is the world market leader in the supply of thermal oil heating systems for ships. This product range includes the Aalborg TFO, an oil or gas-fired thermal oil heater. In addition to the development and production of the thermal fluid heater units, which we supply complete with burner and control system, Aalborg EX is a forced circulation vertical heater for heat recovery from exhaust gases.
This is just a small selection of Alfa Laval’s high-quality product range when it comes to boilers, economizers or heaters. You can find the entire product range, further information and technical details on the Alfa Laval website, or simply call Karberg & Schmitz.
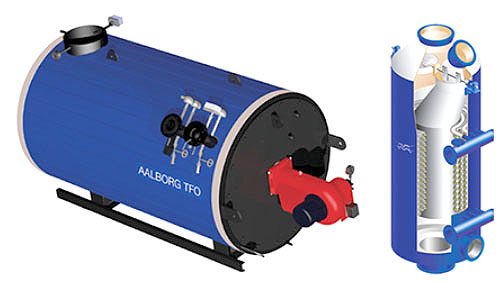
Organic Rankine Cycle (ORC) – Heat to power
The Alfa Laval E-PowerPack uses Organic Rankine Cycle (ORC) technology to convert waste heat into free electrical power, making it a convenient, sustainable solution with a measurable impact on energy efficiency.
Because it works with the low temperature of the engine jacket water (HT), your vessel can generate electricity continuously – from the very first minute. Adding high-temperature steam heat increases its output, which means further fuel savings and even faster payback. The ORC system is designed so that it does not become a hassle for the crew. The ORC system connects and synchronizes itself with the on-board power grid without the need for human intervention. The components have been carefully selected so that we are talking about thousands of operating hours on the first large TBO.
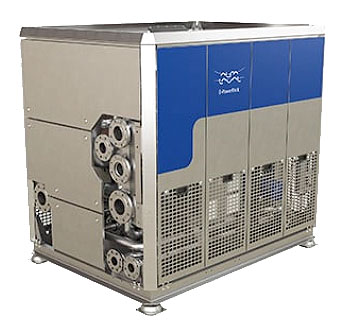
See more at: www.alfalaval.com

Alfa Laval Aalborg
Inert Gas Generators
Alfa Laval Smit Combustion is a saturated inert gas generator with low pressure, which produces inert gas by combusting fuel oil with air controlled combustion chamber.
Smit inert gas generators are typically found on chemical tankers and product tankers. The inert gas generators produces inert gas by combusting fuel oil with air.
Monitored by a specially designed oxygen analyzer and indirectly cooled by seawater, the combustion process is soot-free, thanks to a unique Ultramizing system (blue flame) that ensures complete combustion even in practical-load conditions.
How it works
Fuel oil and air are combusted in the generator to produce hot inert gas with an oxygen content of 2-4%. The combustion process is soot-free thanks to the unique Smit Ultramizing system, which ensures complete combustion even in partial-load conditions down to 25%.
In the scrubber section of the generator, the inert gas is directly cooled by a spray and cooling system, which at the same time washes out the sulphur oxides. The cooled inert gas then flows from the generator to the cargo tank through a deck water seal. This seal is a safety device that continuously prevents any backflow of gas from the cargo tank towards the inert gas system in the engine room. To prevent overpressure or vacuum in the cargo tank, a pressure/vacuum-breaker is installed.

The picture represents a standard Inert Gas Generator (FU type) complete with air fans, fuel pumps, deck water seal and P/V breaker.
Smit LNG
Alfa Laval Smit LNG/LPG is a dry inert gas generator with low pressure and low dew-point.
The most complex inert gas generators are installed on LNG carriers, where very dry inert gas is required and consist of four main components: generator, cooler, chiller and dryer unit.
The cooler, which has gas contact surfaces of SUS 316 for lifetime service, takes up minimal space due to the low-temperature output of the generator. Using water from the chiller, it stabilizes the heat radiation in all conditions.
The dryer unit is redundant and provides additional security. The entire installation is horizontal and allows easy maintenance, although maintenance is seldom required.
How it works
For gas- and chemical transportation the inert gas needs to be of high purity. For many applications, oxygen levels of 0.5% or even 0.1% are required, in combination with a water dew-point of about -45 °C and sometimes lower (-65 °C). Also here, the burner is the heart of the system as the inert gas needs to be absolutely soot free in the first place.
When the gas leaves the generator, it has the right composition, but it is saturated with 100% water and has to be dried.
The drying process takes place in two steps. In the first step of the refrigerant cooler, the gas temperature is lowered to 5 °C which results in condensation of a great quantity of water.
In the second stage the inert gas is dehumidified further in a double vessel type drying unit using activated alumina or adsorbent. The whole process operates under a pressure of about 0.3 bar(g).


Precise Tank Measuring | API MArine
Welcome to API Marine!
API Marine sets the standard by bringing proven measurement technologies of the 21 century into use on tank installations within marine and industry. This provides customers with improved and new higher level of accuracy and efficiency in tank measurements.
UTS™ – Ultrasonic Tank Switch
Universal Level Switch UTS™ has extended operating temperature range from –200°C to +450°C and is designed for level detection in cargo holds, wells & service tanks.
Ultrasonic Tank Switch UTS™ is made of stainless steel and is used for level detection of liquids in vessel tanks, storage tanks, bilge water tanks, cofferdams as well as for control of water ingress to vessel’s compartments.
The operating principle of UTS™ is based on an acoustic wave technology, providing outstanding results in extreme operating temperatures. Accuracy of measurement is ensured regardless of shape of tank, type of liquid or liquid temperature.
UTS™ is installed outside the tank/pipe with only a metal rod inside the tank/pipe. Acoustic waves in the metal rod created by piezo-electric transducer ensure transmission of signals. When liquid in the tank reaches the probe on the rod, the emission of sound waves is muffled. This change is picked up by the piezoelectric transducer and a signal is transmitted to the corresponding alarm. Having only the metal rod inside the tank and no mechanical or moving parts means no maintenance is required.
UTS™ is characterized by high resistance to sticky products, high robustness and shock resistance and increased reliability under dynamic load and vibrations due to reinforced rod and electronic unit of new generation. UTS™ is also supplied in a special “Arctic” version, for applications in harsh environments with ambient temperature of down to –60°C without heating the device.
TLA™ – Tank Level Alarm
Tank Level Alarm is used for detection of high (95%) and high-high (98%) levels in tanks.
Built on the same patented acoustic wave technology as UTS™, TLA™ features high level of accuracy, reliability and customizability.
TLA™ represents a two-point level switch with alarm levels defined by length of rods, which are produced on request. Built-in test buttons are used for performing functionality test before filling in the liquid.

TGD™ – Tank Gauging Device
TGD™ – Tank Gauging Device – a multifunctional deck sensor is designed for simultaneous measurement of level, temperature (up to 15 points), pressure and density (option) in cargo tanks.
Operation principle of TGD™ is based on the patented principle of Guided Low Frequency (GLF™) wave propagation, which allows equally precise measurements along tank height with any shape of tank and type of liquid.

UPT™ – Universal Pressure Transmitter
upt UPT™ – Universal Pressure Transmitter is used for measurement and detection of pressure in tanks and pipeline installations onboard or ashore, for level measurement (hydrostatic method) in service, ballast and slop tanks as well as for draught measurement.
Housing and membrane of UPT™ are made of stainless steel.
Special attention has been given to meeting demands for a high level of enclosure, robust, compact construction and resistance to shock and vibration where conditions of high overload and temperature variation are common.
UPT™ can be specially designed for IP 68 applications and it meets the highest standards and extended requirements for arctic and cold climate operations.
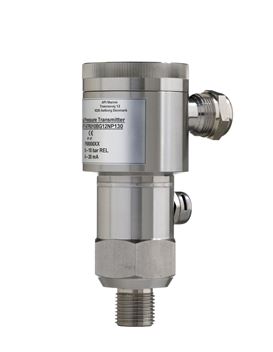
UTT™ – Universal Temperature Transmitter
uttUniversal Temperature Transmitter UTT™ is used for temperature measurement of various media – water, oil, petrochemicals, acids, alkalies, gases and steam. UTT™ is characterized by a reinforced housing manufactured in stainless steel and a possibility of open-air installation.
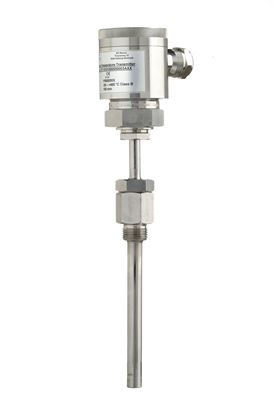
Integrated Automation System
The Integrated Automation System (IAS) provides centralized remote automated control and monitoring, emergency alarm and status alarm of all pumps & valves of ballast and cargo systems, monitoring of loading, stability and floatability, engine appliances and major alarm systems.
The Integrated Automation System is a reliable and powerful tool for safe and efficient vessel operation. The system’s hardware and software are 100% developed and manufactured by API Marine, and it is an “open source” system with the possibility of integrating third-party equipment.

More to find about precise tank measuring: www.api-marine.com
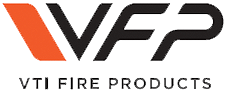
Fire Fighting Systems | VTI Fire products
Who we are …
VTI Fire Products Co Limited is a developer and manufacturer of products for fire extinguishing systems. Based in Shanghai, the company is a joint venture with VTI Fire Products in the UK, where all products are designed and manufactured in an ISO 9001 certified production facility.
The product portfolio covers comprehensive fire protection solutions, including
- Deck Monitors, fixed and moveable
- VTI-1230
- Sprinkler systems
- INERGEN(IG541)
- High Pressure CO2
- Water mist systems for local application
- Low and high expansion foam
- Water mist systems for complete flooding
What we do…
Our main objective is to promote the research, development and use of various fire protection solutions throughout the world. We will promote our concept to the entire fire and security industry, potential users and authorities.
VTI operates in-house research, development and manufacturing facilities for all products to ensure uncompromising performance and to secure our technological leadership in the future.
All our employees have started to transform our role from a traditional workshop to a modern industrial company. We strive to be recognized as an innovative and customer-oriented company.
Our aim is to develop, produce, sell and service cost-effective fire protection solutions that provide the greatest possible safety for human beings and reduce damage to ships to an absolute minimum.
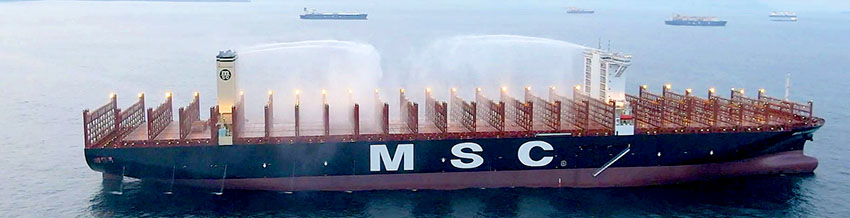
More hot news under: www.vtifire.com

Atlas Incinerators
Incinerators
Since 1974 Atlas Incinerators has been manufacturing incinerators for the marine and offshore market and in that time we have strived to build quite simply the best marine incinerator on the market.
This has led to numerous design improvements over the years. With over 9000 units delivered, mainly to the marine market, we can justifiably claim to be the No. 1 choice for ship owners.
The X10 Titan is our latest series of incinerators, named after the Titans of Greek mythology, known for their great achievements. The series builds on all the successful features that our Atlas series is known for in the market, and adds a number of upgrades based on the latest technology.
The benefits at a glance:
- Only one burner or one burner fits all = significant savings on spare parts compared to having multiple burners. Atlas has developed its own sludge burner without rotating parts.
- Atlas incinerators are designed for the simultaneous incineration of sludge, oil and solid waste.
- Induced draft air ejector for the evacuation of flue gases; hence no flue gas fan is required for the classic ATLAS series.
- A separate settling tank is not necessary.
- No heating of the sludge oil tank necessary.
- Burning oil sludge with up to 50% water without pilot fuel – guaranteed
- Three chambered design – clean burning.
- Most eco-friendly incinerator, as less carbon and carbon dioxide is released into the atmosphere. Contribution to decarbonisation.
Incineration process shortened
The entire incineration process has been simplified and shortened, with several processes that occur in conventional incineration plants now being redundant (see illustration below).
The entire incineration process has been simplified and shortened, with several operations that occur in conventional incinerators now being redundant (see the illustration below).

IT’S OFFICIAL: SLUDGE OIL HEATING IS HISTORY
The sludge oil is pumped directly from the sludge oil tank to the oil burner before combustion, without the need to heat the sludge oil first. In other words, there is no need to use steam, electricity or thermal oil to heat the system. You can see immediate savings in operating costs as heating is no longer required.

Learn more about the most reliable waste disposal under: www.atlasinc.dk

azienda Chimica Genovese (ACG)
ICCP & MPGS
ACG is an Italian supplier of equipment for the marine industry. In 65 years of activity, ACG has installed more than 28.000 units of Anticorrosion (ICCP) and Antifouling (MGPS) Systems and is known as one of the most competitive and reliable manufacturers of electrochemical systems (ECOLCELL).
ECOLCELL – Electro chlorination
Antifouling treatment based on electro chlorination has proved to be the most efficient and the most economical solution.
ECOLCELL electro chlorination system combats macro fouling same as copper anodes and combats in addition micro fouling in the seawater lines on board of ships, oil-rigs and power plants.
Marine fouling, shellfish, seaweed, slime, bacteria, etc. find their way into sea water cooling systems on board usually as micro-organism, settles and grows and if not combated in-time go on to block pipes, filters, valves, intake grids, heat exchangers etc.
ECOLCELL operates by using an electrolytic cell containing Titanium anodes in mixed metal coating (MMO) to transform the Sodium Chloride (NaCl) in seawater into Sodium Hypochlorite (NaOCl) through a process of electrolysis. The antifouling agent is injected into the sea chests from where it is dispersed through the whole sea water system. Only a small concentration of this Sodium Hypochlorite is required to combat marine fouling, normally inbetween 0.1 to 0.3 ppm.
The system operates on the principle of electrolysis: a low voltage is applied to seawater circulation in a cell, producing Sodium Hypochlorite without any addition of chemical products.
No Macro Fouling
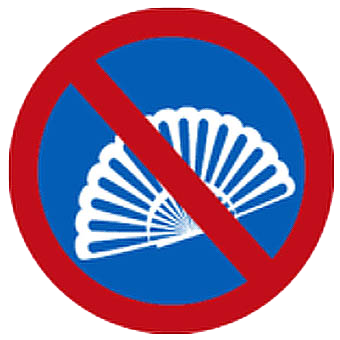
No Micro Fouling

Clean Pipework

Energy Saving

Eco-Friendly

COPRON – Antifouling
ACG also developed a traditionell antifouling system, COPRON, based on Copper & Aluminium Anodes mounted in the sea chest or sea water filter, to prevent marine fouling inside of the cooling sea water circulation.
How it works
As copper is a more noble metal than the material used in the pipe-work, the presence of copper ions in the seawater will cause galvanic corrosion of the pipes, but by fitting an aluminium (Al) or iron (Fe) anode in close proximity to the copper anode, one can achieve some corrosion control by creating an anti-corrosive layer on the internal surfaces of the piping.
As they are installed in the sea chest, they have to be replaced during dry-docking. Hence, the anodes are usually designed for a lifetime of 2-3 years up to 5 years.
The cost of replacement represents considerable maintenance costs, unfortunate often neglected by the ship owners when evaluating the costs of various systems.
No Micro Fouling
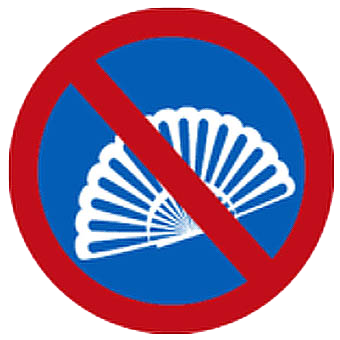
Return of investment

EU-Directive
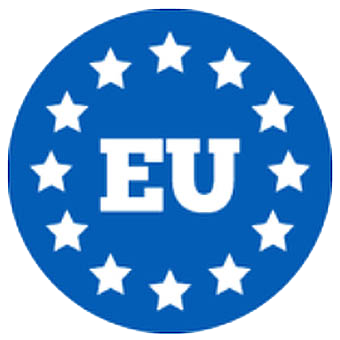
MARIMPRESS – Impressed current cathodic protection (ICCP)
MARIMPRESS ICCP is used to protect ships‘ hulls, floating dry-docks, oil-rigs and other submerged steel structures from corrosion.
The system operates by continually measuring the potential of the submerged steel surface using hull-mounted Zinc reference electrodes. If this potential starts to rise above the preset value, the rectifier supplies the correct amount of DC current to hull-mounted activated Titanium anodes needed to maintain the preset value. In this way, not only the hull, but when technically earthed also the rudder, propeller, shaft and stabiliser fins are protected from corrosion.
This system uses Titanium MMO coated anodes as opposed to sacrificial Zinc or Aluminium anodes, which last longer and cost less to replace.
MARIMPRESS makes use of titanium anodes which give the system a life of more than 10 years.
Green Chemistry

No Corrosion

Economic
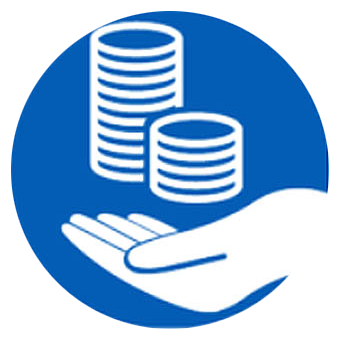
Long Lasting Anode
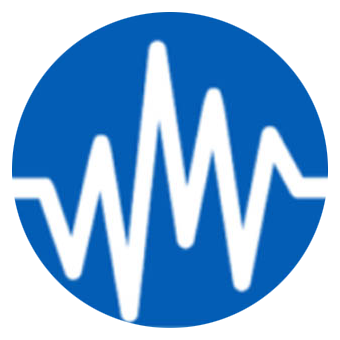
For more information please check: www.acgmarine.com

HVAC&R and fans | DMA Marine
The specialist in marine and offshore HVAC systems
DMA Marine, a subsidiary of Dan Marine Group Ltd, since 2003 has been a leading system designer, manufacturer and supplier of marine heating, ventilation, air-conditioning & refrigeration systems as well as MGO chiller systems for more than 3,000 ship sets for the Chinese shipbuilding industry, which are used on ships by shipowners all over the world.
DMA was the predecessor of the OEM manufacturers of marine air conditioners founded in 1997 and has more than 20 years of experience in manufacturing high-quality equipment in this sector.
A team of about 100 employees consists of qualified equipment designers, experienced service and R&D engineers, a strong project management team and a highly qualified professor from Shanghai Maritime University who provides technical expertise and consultancy services for our HVAC products.
Engineering and System Design
DMA provides tailor-made and optimized solutions for customers based on professional system software, including: Heating and Cooling, Heat Load, Air Flow, Pressure and Noise Calculation, Space Optimization, etc.
Components and Subcontractors
DMA uses well-established and well-known brands as major subcontractors, including: Bitzer , Carrier, Bock, Danfoss, Alfa-Laval, Kruger, Nyborg, ABB, Siemens, Schneider, APV, SWEP, Halton, Desmi, Cloriu, Belimo etc.
Commissioning and Service
About 50 service engineers and service partners take care of customers’ needs around the clock.
Air Handling Units

Water Cooled Condensing Unit

Deck Units

Cabin Unit

Packaged Air Condition Unit

Provision Refrigeration Plant

centrifugal fan
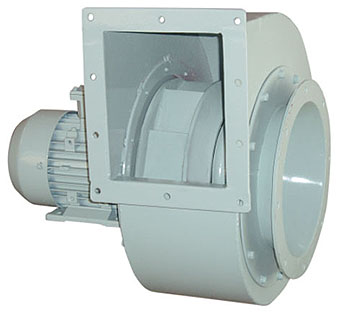
Marien Axial Fan
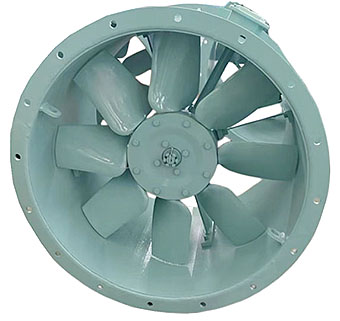
Open type axial fan
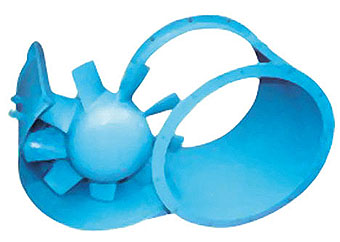
For more information please use following links: www.dma-marine.com
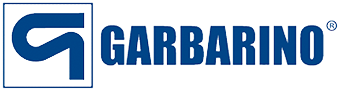
Centrifugal pump | Pompe Garbarino
The family-owned manufacturer of who keeps the complete production process in house
Founded in 1932 by Paolo Garbarino, Garbarino maintains its “core business” in the marine, offshore and naval fields.
Instead of adopting mass production methods, Garbarino has chosen the technological search in sophisticated and demanding fields. The attention is focused on the constant improvement of the products designed according to the customer’s requirements and selecting the most suitable materials for the different applications.
Garbarino offers an excellent service to customers in terms of technical consultancy and after sales service ensuring the availability of engineers on site. Spares delivery and product replacement can be guaranteed in very short time thanks to the huge capacity of the warehouse, one of the best strength’s points of the company.
Marine field
Supplier of major shipyards in Europe and Asia, ship owners worldwide, world market leader in cruise shipbuilding.
Naval field
Official supplier of the Italian Navy since 1950, supplier of several foreign navies.
Industrial field
Pumps specifically manufactured for industrial applications and different type of plants who apply centrifugal pumps in their daily operation.
Horizontal pump
Use
Fresh and sea water, condensate, oils, chemical and petrochemical products.
Main Features
Pump: centrifugal type, end-suction single volute casing, single flow and axial inlet.pump
Impeller: high efficiency, close type, statically and dynamically balanced. Low axial thrust thanks to impeller provided with balancing holes.
Mounting system: shaft supported by radial and thrust type bearings placed in an oil bath bracket or, upon request, by self lubricated or grease lubricated ball bearings.
Seal: single mechanical seal to DIN 24960. Special mechanical seal or cartridge type for specific application or aggressive liquids. Possibility to install soft-packing with external flushing.
Self-Priming
Small and medium size pumps can be equipped with built-in priming element; all sizes can be supplied in self-priming version with an additional air ejector.
Back pull Out
It is possible to remove the rotating components without disturbing pipes, pump casing and motor by using a flexible spacer coupling.
Base Plate
The base plate is generally built of welded steel and it can be provided with drain-pan for possible drippings.
To comply with special requirements (nonmagnetic and/or anti vibration) it can be manufactured in stainless steel (AISI 316) and equipped with anti-vibration and/or anti-shock resilient mountings.
Special Versions
Special versions according to Naval Rules are also available: shock-proof, vibration-proof, noise-proof, nonmagnetic.

Vertical Inline Pump
Use
Fresh and sea water, condensate, oils chemical and petrochemical products.
Main Features
Pump: centrifugal type with volute casing, vertical construction, single stage, single flow, in line flanges.
Impeller: high efficiency, close type, statically and dynamically balanced. Axial thrust balancing by means of annular chamber with balancing holes located behind the impeller.
Mounting system: shaft supported by radial and thrust ball bearings either grease or self-lubricated.
Seal: single mechanical seals to DIN 24960. Special mechanical seals or cartridge type, for specific application or aggressive liquids. Possibility to install soft packing with external flushing.
Self-priming: some listed models can be supplied with a self-priming element either with liquid ring or with air ejector.
Back Pull Out
It is possible to remove the rotating components without disturbing pipes, pump casing and motor by using a flexible spacer coupling.
Base Plate
The base plate is usually cast with pump casing for small and medium size pumps in order to increase the structural stiffness. For larger pumps a welded steel base plate is provided.
Motor Frame
The motor frame supporting the electric motor is normally made of welded steel.

Recessed impeller torque flow pumps
Description
Thanks to the shape of the impeller and to its recessed position in the casing, MCA pumps are suitable for pumping viscous and pasty liquids containing suspended solids.
Main Features
Impeller: the impeller is of open type with radial blades. The impeller is provided with vanes to balance the axial thrust and the pressure in the stuffing box area.
Casing: volute type with ample section end suction and top discharge nozzles. The flanges are NP 10 according to UNI-EN-DIN-JIS- standards.
Shaft sealing: basic pump version is mechanically sealed but soft packing with optional external flushing with clean fluid can be fitted. In case of dangerous liquids pumps can be provided with double mechanical seals completed with barrier system. For high temperature the pump can be provided with a cooling chamber. The fitting of single or double acting mechanical seals flushed from external source by suitable media can also be possible.
Materials
Standard constructions are in cast iron, carbon steel, stainless steels. Any other material combinations can be supplied.
Performances
Capacity up to 500 m3/h.
Total dynamic head up to 100 meters.
Speed from 750 to 3500 rpm.
Working Principle
The special impeller shape and its position in the back part of the casing operates in such a way that the solid particles in suspension flow through the casing without touching the impeller directly.

Side Chanel Pump
Design Feature
BT pumps are self-priming side channel multistage pumps. The impellers are star shaped, balanced to reduce axial thrust on the bearings. Bearings are external, life grease lubricated. The pumps have a very low NPSH value that allows operation with suction lift up to 8 meters. Basic design pumps are mechanically sealed. It is possible to fit double mechanical seals when handling hot liquids which may solidify, toxic, aggressive and corrosive media. In this case the seals are flushed from an external source with a fluid compatible with pumped medium at a slightly higher pressure.
Operating Pressures and Temperatures
Up to 120°C: 40 bar
Above to 120°C: 16 bar
Max operating temperature: with mechanical seal 160°C
Minimum operation temperature: -10°C
Materials
Construction is provided in the following materials: cast-iron, different types of bronze and stainless steel. Special constructions according to Naval Rules: shock-proof, noise-proof, vibration-proof, nonmagnetic versions.

For more Information please visit: www.pompegarbarino.com

Leistritz
Screwpumps
The international requirements for the operational reliability of ships and machines in the shipbuilding and marine sector as well as the general conditions and limitations regarding energy efficiency and the emission of pollutants are constantly increasing. Leistritz has already been meeting these rising requirements for decades.
Robustness and production quality as well as long service lives and availability are the attributes which have always been associated with Leistritz screw pumps on the market. In order to be able to guarantee and document a consistent product quality, each Leistritz screw pump is thoroughly tested under the specified operating conditions on our test stands.
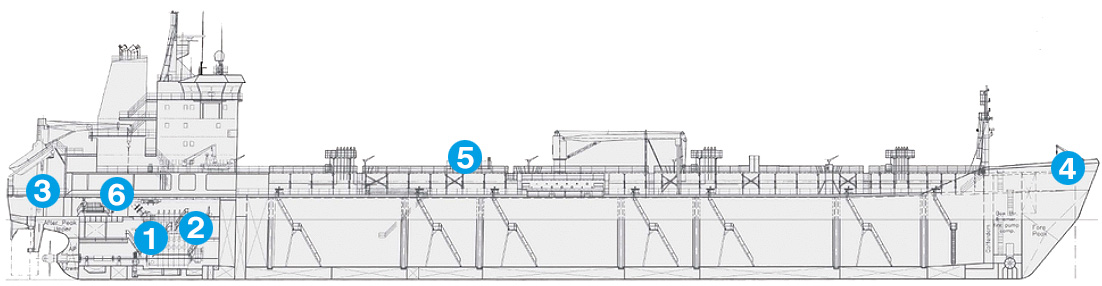
(1) Schmierölsystem für Maschinenräume
Hauptschmierpumpe für Dieselmotoren
Transfer Pumpe für Schmieröl
(2) Heizölsystem für Maschinenräume
Versorgungs- und Zirkulationspumpe für Brennstoffmodule
Transfer Pumpe für Diesel- und schweres Heizöl
(3) Ruderanlagen und Verstellpropeller
Hydraulikpumpe für Verstellpropeller und Ruderanlagen
(4) Winden
Hydraulikpumpe für Winden
(5) Loading and Unloading
Ladepumpe zum Be- und Entladen von Tankern
(6) Sonderanwendungen
Maßgeschneiderte Lösungen mit Schraubenspindelpumpen
L3N screw pumps
Leistritz screw pumps in the L3N range are three-spindle, single-volute, self-priming displacement pumps for the low-pressure range. They are used to transport non-abrasive lubricating fluids.
Cargo application
A wide variety of specialized vessels are generally used for the transportation of liquid freight on inland and shipping routes. In order to be able to safely load and unload the freight, these ships must be adapted for the specific storage and transport features. The same applies for the pumps which are used here. They have to ensure reliable and safe operation for a wide range of viscosities, temperatures and other operating conditions and influences. Here, Leistritz screw pumps offer optimal volume stability, robustness and operational reliability for almost all liquid freight goods and products.
L4 screw pumps
Leistritz screw pumps in the L4 range are twin-screw, double-volute, self-priming positive displacement pumps. They are used to pump aggressive / non-aggressive, abrasive / non-abrasive low to high-viscosity fluids with lubrication / non-lubrication properties. The spindles are manufactured in one piece which leads to low rotor deflection and non-contacting design. The special spindle geometry minimizes pulsation and optimizes the NPSH value.
The arrow-toothed gears helps to reduced the noise level. The advantages of the replaceable insert is easy to see in the low-maintenance.

L3N Screw pump

L4 Screw pump

For more Information please visit: www.leistritz.com

Netzsch
NEMO® Progressing Cavity Pumps
NEMO® Progressing Cavity Pumps have a very broad application range and are used in all branches of industry for the continuous, pressure-stable, gentle and low-pulsation conveyance of almost any substance.
Whether for sludge, chemical substances, adhesives, petroleum or yogurt, one of the pump types by NETZSCH in various rotor/stator geometries and a selection of engineered joints make sure to suit your application.
The pumps are at home where a great variety of different substances must be pumped or very precisely dosed. From low viscosity media to products barely capable of flowing, with or without solid content, shear-sensitive, sticky or abrasive.

Features of the NEMO® BY Progressing Cavity Pump
- continuous low-pulsation conveyance unaffected by fluctuations in pressure and viscosity
- conveyance volume in proportion to rotation speed with high dosing precision over the entire rotational-speed range
- high pressure capability without valves
- location of the mechanical seal directly under the intake port in the pumping space makes external flushing of the seal unnecessary in many applications
- short drive shaft and pump lantern offer high stability for mechanical seal installation
- separate flange bearing and pump base make it easy to change the stator
More to find under: www.pumps-systems.netzsch.com
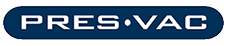
P/V Valves | Pres-Vac
At Pres-Vac Engineering, we Speak Marine
For already more than 50 years, Pres-Vac Engineering has been a renowned brand in the marine industry. We have installed over 200,000 valves and are the largest supplier of high velocity pressure/vacuum valves and venting systems for the transportation of volatile organic compounds (VOC).
Thanks to our experience, we can always offer the best solution for your specific tank venting requirements. Our solutions are innovative, reliable, extensively tested, tailored to your specific needs and always comply with all standards and regulations. We offer you unrivaled experience, advanced research and engineering capabilities, worldwide service and support, and a global network of representatives, agents and partners.

PV-ECO & PV-VOC
The PV-ECO and PV-VOC have been designed based on the experience gained by Pres-Vac over the last 60 years. They have been designed using the latest technologies, but most importantly the PV-ECO and PV-VOC have been designed based on customer feedback.
PV-ECO: The Chemical Tanker P/V Valve
The PV-ECO is designed for use on chemical carriers and product carriers. It has been approved for long pipes, which increases flexibility in the design of pipelines for the shipyard. Compared to the previous generation, we have simplified maintenance by reducing disassembly time by 60% through a reduced number of parts.
PV-VOC: The Crude Oil Tanker P/V Valve
The PV-VOC has been developed to meet the requirements that larger crude oil carriers have for P/V valves. The PV-VOC is designed to reduce the amount of cargo vapor by implementing a special 2-step opening sequence.
PV-Methanol: The P/V valve for methanol bunker tanks
Pres-Vac is the first supplier of PV valves to help ship owners overcome the challenge of handling methanol in their own bunker tanks. The methanol tank system typically consists of storage tanks, service tanks and drain tanks and is usually installed at the bottom of the engine room. Long vent lines dealing with positive and negative pressure must be able to protect and breathe at the same time. Special PV valves developed by Pres-Vac are one solution.


Air caps and Air Release / Vacuum Breaker Valves
Air caps and air release/vacuum breaker valves serve two purposes: they vent the tank and prevent water from entering the tank. Air caps are installed on the air lines of the service tank. A wire mesh prevents flames from entering the tank. Pres-Vac offers the following air caps and vent/vacuum breaker valves.
Liquid Overfill Protection Devices
Liquid overfill protection devices are designed to prevent tanks from becoming pressurized due to overfilling, which can occur if the high-level alarm float is punctured. Failure to use an overfill protection device can cause the tank to burst and lead to massive contamination.
Onboard Test Rig
On-board test rigs are used to verify the set pressure after maintenance as well as to check for and measure leakage.

More to find at: www.pres-vac.com

Oxymat Nitrogen
Solutions for inert gas and duel-fuel Engines
With an intertgas nitrogen generator solution from OXYMAT you have nitrogen when and where you need it.
OXYMAT is a pioneer in designing and manufacturing on-site oxygen and nitrogen generators, using pressure swing adsorption (PSA) technology since 1978. With our track record comes first hand knowledge of the market, development, demands and the possibilities the PSA technology holds. Recently we have broadend our portfolio to include flexible N2 generators based on membrane technology.
Here to guide you
While the sales and service activities are coordinated from Denmark (HQ), the production team in Slovakia will assemble and fully test (FAT) the units in their own quality production facilities.
Wide Range of vessels
The OXYMAT nitrogen solutions are suitable for many applications on gas carriers, chemical tankers and dual fuel vessels e.g.:
- Purging fuel gas system and cargo piping
- Pressurizing of the barrier insulation spaces and cofferdams
- Seal gas for LNG boil off gas High Duty (HD) and Low Duty (LD) compressors
- Blanketing of explosive, flammable or toxic cargo to O2 ppm levels
- Padding of fuel tanks
Key features

THE RIGHT CHOICE OF SYSTEM
Flexible membrane solutions | perfect for retrofit
- Space optimized Fits into ana space
- World’s smallest footprint @ 635 m3/h Nitrogen production on the fly
- Optimized controls
- Minimum maintainance
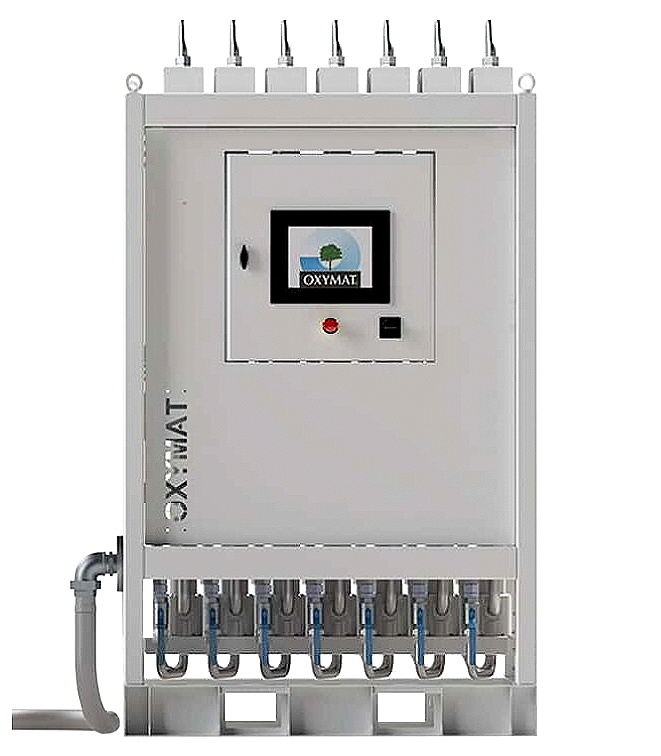
Optimized PSA solution – NORDIC SERIES | best in class
- Energy optimized
- Smaller compressor for same capacity
- Less carbon molecular sieve (CMS) for same output Flow capacity more than 4,500 m3/h
- Designed optimized for extended lifetime Low opex

Industry standard PSA – TWIN TOWER | low TCO
- High N2 purity higher than 99.9% (ppm level) 2-column system
- Control panel and 7” screen
- Purity monitoring and alarm settings as standard Advanced control system as costomized solution
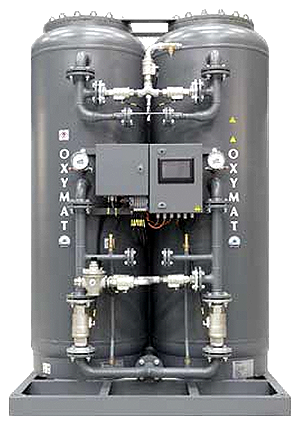
More about N2 generators to be found under: www.oxymat.com